DensFlow –
Flow metering in dense-stream
The measuring system for continuous flow metering in dense-stream conveying
and high levels of throughput
- Reliable flow metering in pneumatic dense-stream
- Unlimited throughput volumes can be measured
- optionally pressure-resistant up to 25 bar
- Installation creates no obstacle in the profile, hence no dead spots in which residue can form
- Measurement independent of the flow speed of the material
- Simple retrofitting
- Maintenance-free
- Contactless measuring procedure (no mechanics)
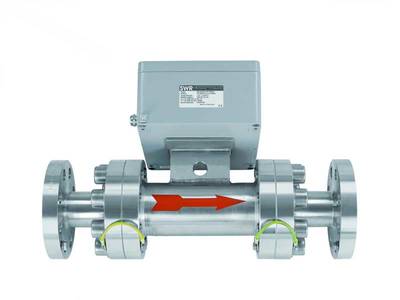
What do you want to do?
Use
DensFlow is a measuring system specially developed for flow metering of solids in dense-stream conveying. DensFlow is used in the online measurement of:
– Powders or granules
– in pneumatic dense-stream transport
Function
The SolidFlow 2.0-sensor uses the latest microwave technology.
The sensor is used exclusively in metal piping.
The measuring field is generated through the special coupling of the microwave together with the metal pipe.
The microwave coupled into the pipe is reflected by the solid particles and received by the sensor.
The received signals are evaluated with regard to their frequency and amplitude.
The sensor virtually works like a particle counter that counts streaming particles per time unit.
The frequency-selective analysis ensures that only streaming particles are measured.
The SolidFlow 2.0 has a active roping compensation. Based on latest microprocessor-technology, the measuring signal is being dismantled in its frequency spectrum, which enables the sensor to compensate influences of roping.
The calibration of the sensor takes place in the installed state, simply by pushing a button and entering the reference quantity.
Mounting and Installation
For the assembly of the sensor, the installation location is specified in accordance with the conveyed inlet and outlet paths.
In case of pipe diameters over 200 mm, 2 or 3 sensors per measuring point are used, with the sensors arranged at 90° or 120° to each other.
In free-fall applications (e. g. after conveyor screws or rotary conveyors), an inlet path (fall height) of at least 300 mm is ideal. Shorter inlet paths are possible by agreement.
The sensor bracket (welding socket) is welded on at the specified installation location. After this, a 20 mm-borehole is drilled through the sensor bracket and through the pipe wall.
The sensor is then adjusted to the wall thickness, inserted and fixed with the help of the coupling nut. Done!
Commissioning:
The commissioning of the measuring device takes place via the FME analysis electronics.
These electronics offer a convenient, menu-driven input of parameters such as measuring range, desired physical units or measuring signal attenuation.
The available outputs are a current output, 4…20 mA as well as a pulse output (open collector). The menu language options are German, English or French.
Technical Data
Sensor | Housing | Stainless Steel 1.4571, NW 10 … 125 mm, flange EN 1092-1 | |
---|---|---|---|
Inner pipe | Ceramic | ||
Protection category | IP 65 according EN 60 529/10.91 | ||
Environment temperature | Sensor pipe electronic: – 20 … + 60 °C Sensor pipe: – 20 … + 80 °C (higher temperatures as option) |
||
Max. working pressure | 16 bar, optional 25 bar | ||
Working frequency | 100 kHz | ||
Weight | Depending on the nominal diameter | ||
Velocity range | 1 … 10 m/s | ||
Accuracy | ± 2 … 5 % in the calibrated range range | ||
Dimension | NW + 90 mm, L 500 mm | ||
Transmitter | Power supply | 110 / 240 V, 50 Hz, 24 V DC | |
Power consumption | 20 W / 24 VA | ||
Protection category | IP 65 to EN 60 529 / 10.91 | ||
Operating temperature | – 10… + 45 °C [14 … 113 °F] | ||
Dimensions | 258 x 237 x 174 (W x H x D) | ||
Weight | approx. 2.5 kg | ||
Cable glands | 3 x M 16 (4.5 – 10 mm Ø) | ||
Terminal clamp wire size | 0.2 – 2.5 mm² [AWG 24-14] | ||
Current output signal | 2 x 4 … 20 mA (0 … 20 mA), load < 500 | ||
Alarm output – Error output | Relay with toggle switch – max. 250 V AC, 1 A | ||
Data backup | Flash memory | ||
Impulse output | Open Collector – max. 30 V, 20 mA | ||
RS 485 interface | ModBus | ||
Application Examples
Click on a desired application example to navigate to a detailed description.
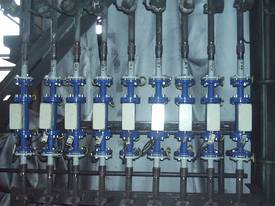
Flow metering of coal dust
in dense streams in steel manufacture
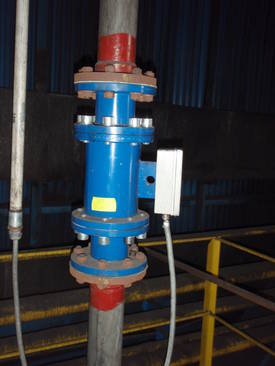
Flow metering of coal dust
in dense streams in a steel plant
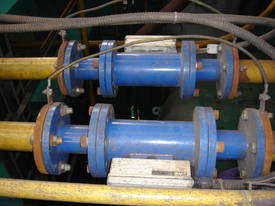
Main lance monitoring
during coal injection in the steel plant
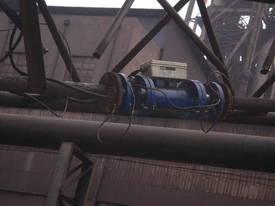
Single lance monitoring
in the steel plant during the firing of the oven
Global Technology Systems
P.O. Box 799 Shalimar, FL 32579. USA
(850) 651-3388
[email protected]